The Weekly Reflektion 13/2023
Before any critical activity a risk assessment is normally carried out to ensure the hazards associated with the activity are identified and the risks from carrying out the activity are acceptable. Similar activities may have been carried out before and it seems appropriate to review previous risk assessments to gain the benefit of any experience transfer. However, it may not be appropriate to use previous assessments directly as conditions and circumstances may have changed since the last time. Assuming everything is the same as last time is one step towards a disaster.
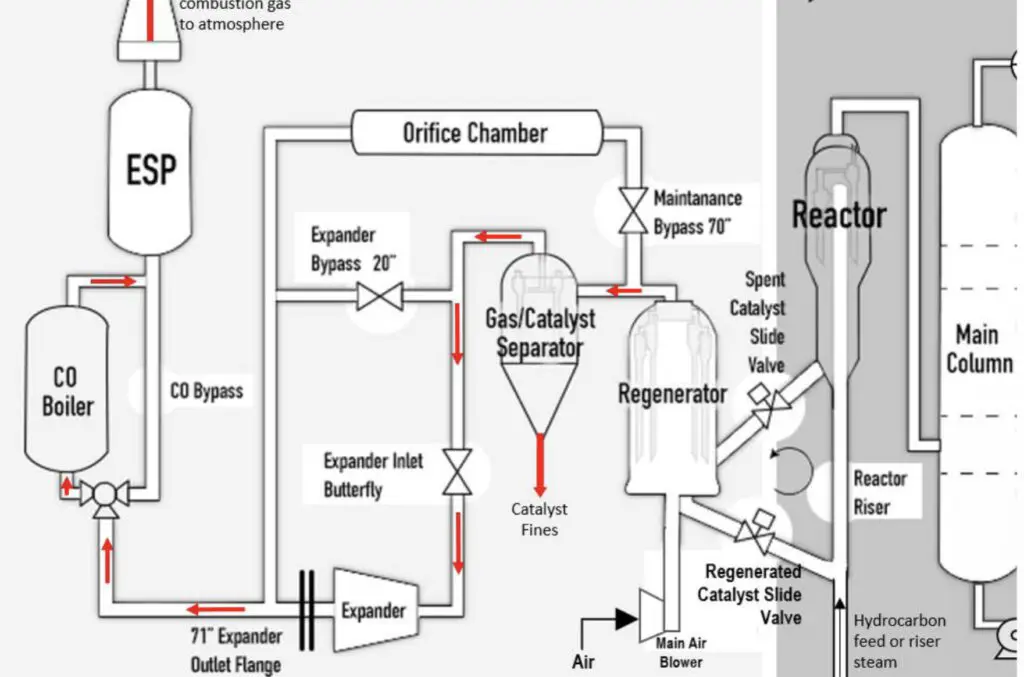
Do you cut and paste from previous risk assessments and assume then that the outcome will be the same?
On Wednesday 18th February 2015 an explosion occurred at the Torrance Refinery located just outside Los Angeles in California. At the time of the explosion the refinery was operated by ExxonMobil. The explosion occurred in the Electrostatic Precipitator (ESP), a pollution control device in the fluid catalytic cracking (FCC) unit that removes catalyst particles using charged plates that produce sparks—potential ignition sources—during normal operation.
The reactor in the FCC is used to convert heavy hydrocarbons into lighter hydrocarbons. During the operation coke forms on the catalyst and has to be removed. This is done by taking the FCC offline and using steam to create an overpressure to prevent hydrocarbons entering the reactor. Two slide vales are opened to dump the catalyst into a regeneration system where the coke is burned off using hot air. The hot air is then passed through the ESP to remove any small particles of catalyst. The ESP generates sparks that could provide an ignition source so it is important that hydrocarbons do not enter the ESP.
A vibration problem with a turboexpander on the regeneration cycle occurred on 11th February 2015 and a repair was initiated that required the FCC to be shut down and pressured with steam and the turboexpander isolated. A similar problem had occurred in 2012 and a variation request had been raised and approved for the task. The variation request was essentially a deviation from the isolation procedures and included a risk assessment for the work. This task had been carried out successfully. The refinery personnel decided to use this deviation and the associated risk assessment in the planning of the turboexpander repair.
During the task there were problems installing an isolation spade in a flange and the steam rate was reduced. This lowered the pressure in the FCC and allowed hydrocarbonsfrom the process system to enter. One of the slide valves was leaking, most likely due to erosion from operating with the solid catalyst present. Hydrocarbons leaked through the slide valve into the regeneration system (air side in figure) and eventually reached the ESP where they exploded. In 2012 there were no problems reported with installing the flange. A leaking slide valve was not identified as a potential problem in the 2012 risk assessment.
One of the challenges in using risk assessments from previous seemingly similar tasks is that the outcome from these tasks is often good, that is completed successfully This can lead the people involved in the risk assessment to assume that following the same process will give the same outcome. In the case of Torrance refinery this assumption led to an explosion that luckily did not have fatal consequences.