The Weekly Reflektion 47/2021
Having control of hazardous materials is an important first step in preventing many types of incidents.
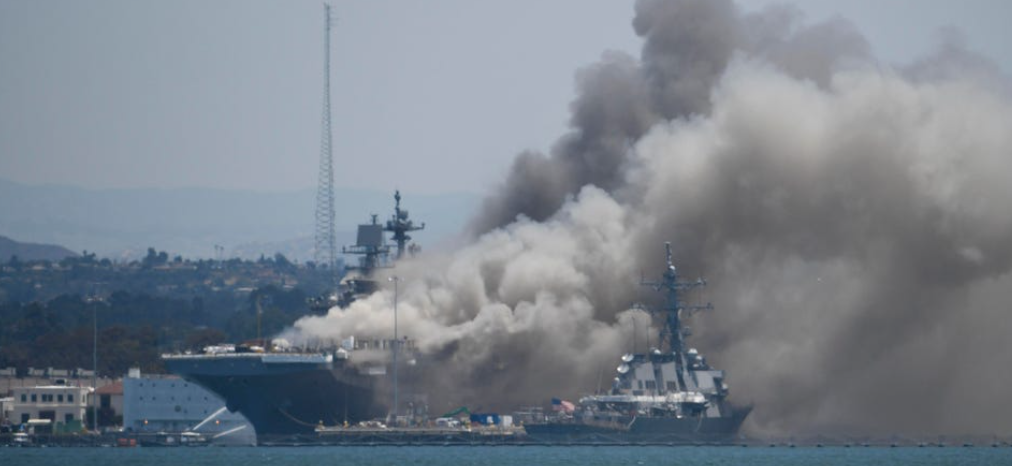
How do you ensure the training and behaviour of the people at the worksite meets your expectations?
On the 22nd of May 2008, a fire in a storage area on the nuclear-powered aircraft carrier, the USS George Washingtontook 12 hours to extinguish, injured 37 fire fighters and caused US$70 million in damage. The investigation concluded that the fire was ‘entirely preventable’.
At 0600 hrs the first report of ‘smelling smoke’ came into the control room, and the initial suspicions were directed at the ship’s incinerator. This was checked and found to be OK. At 0745 hrs white smoke was observed, and the order came to shut down the incinerator as a precaution. In the next 35 minutes, eight smoke observations from various locations around the ship were reported and the ship’s general alarm was sounded at 0820 hrs. The location of the original fire was finally determined 8 hours after the first smoke was noticed as an unmanned space called the auxiliary boiler exhaust andsupply space. By this time the fire had spread to 8 decks and 80 compartments. Drawings that had not been updated after modifications, and a crew with inadequate knowledge of their ship also contributed to the confusion.
One month before the fire, the chief engineer had foundapproximately 350 gallons of flammable refrigerant compressor oil in this same compartment. This was a hazardous material and should have been stored in the HazMat storage area. Orders were given for the oil to be removed, and the removal had been confirmed, but the investigation found that there was still 115 gallons of oil in this storage space at the time of the fire. Also stored in this space were technical publications and lagging materials, both unauthorised, and flammable. Other examples of hazardous material being stored around the ship were also common.
Cigarette butts were found adjacent to an exhaust fan that led to this storage compartment. The three theories concerning the start of the fire were a lighted cigarette, self-ignition of the oil, or an electrical failure. The oil, the technical documents and the lagging fuelled the fire, which then ignited the fibre optic and electrical cabling.
The damage control department on the ship had been audited and found deficient on 3 previous inspections between June 2007 and April 2008. The function of the damage control training team (DCTT) was to provide training for the crew, and to hold exercises and drills. They were found to be ‘ineffective’ during a drill, and concerns were expressed about the DCTT’s ability to train the crew in basic damage control. Of the entire ship’s crew, 85% had attended general shipboard firefighting, but only 35% of those required to have had the advanced firefighting course had been trained. A program had been started to improve the crew training around numerous processes and procedures related to fire prevention readiness,but the investigation found this was ‘too little, too late’.
Does your operation ensure that there is strict control of hazardous materials? How do you ensure that ignition sources and flammable material are separated? Do you have a good system for correcting deficiencies in qualifications and training in your emergency response organisation?