The Weekly Reflektion 33/2021
The Pryor Trust blowout in 2018 in Oklahoma, USA, killed 5 people. These deaths could and should have been prevented. What can we learn from this Major Accident?
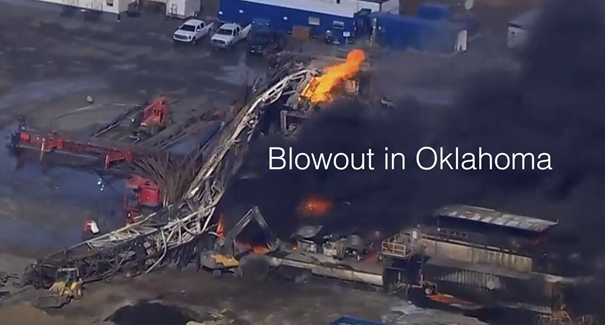
Why did the operational team believe what they were doing was OK?
On January 22nd, 2018, a blowout and rig fire at a Pryor Trust gas well in Oklahoma, USA, killed 5 rig workers trapped in the driller’s cabin on the rig floor. The chain of events leading to the blowout were described in last week’s Reflektion.
In all investigations Reflekt has performed, and those we have studied, the involved personnel make decisions that they believe are correct at the time. In the case of the Pryor Trust blowout, significant pit gains were seen from examining the data after the incident. Why were these pit gains, a strong signal of a well control issue, not reacted to?
The US Chemical Safety Board (CSB) investigation found that there were no procedures for pulling out of hole using the ‘calculated fill’ method employed. This method involves pumping a calculated amount of mud back into the well equal to the volume of steel drill pipe pulled from the well. The rig crew had not done this before, and, having no procedures, were exposed to possible mistakes and misunderstandings. Implementation of new ways of working requires effort and care.
The alarm system did not differentiate between critical and non-critical alarms, leaving it up to the individual to do this manually. It is perhaps understandable that the driller may have disabled the alarms to prevent distraction.
Gas was being flared as drilling was progressing, which seems to be another sign of a well control issue. In drilling operations where many similar wells are drilled back-to-back in the same formations, experience leads to fine-tuning procedures. In some gas wells, significant amounts of drilled gas, that is gas contained in the formation that is being drilled by the bit, can be released, and may need to be removed from the mud using the mud-gas separator. High drilled gas does not necessarily mean that the well is underbalanced. The trap of assuming the well is the same as the last one may have come into play, given the often-wrong assumption that what worked last time will work again, or ‘outcome bias’ in an investigators world.
Flow checks are a normal tool in the toolbox to ensure that a well is stable and still in an overbalanced situation. The CSB investigation found that on this well and the previous well drilled by the rig, only two out of the 27 flow checks required by the rig contractor management system had been performed, and these two had been ‘inadequate’, such as the 45 second flow check mentioned in the chain of events. An operator with a focus on saving rig time, may have turned a blind eye to the practice, so it became the way things are done on this rig, a ‘normalisation of deviance’.
Considering lack of procedures, outcome bias, and normalisation of deviance, it is perhaps not difficult to explain why the involved people did what they did and why the thought it was OK. The crew and the operator had perhaps lost focus on the real dangers involved in drilling operations.
Next week we will address the regulations and the part the operator played in the blowout.