The Weekly Reflektion 29/2021
What is the worst Major Accident we have come across? What criteria should we use to judge the many Major Accidents that we have studied? The consequences in the terms of loss of life, impact on the environment or financial loss? In our view it is more appropriate to judge based on the failure of the systems in place to prevent a Major Accident.
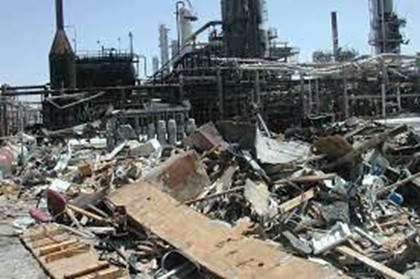
What signals were ignored prior to the Texas City Refinery disaster in 2005?
The Texas City Refinery explosion in 2005 is one of the worst Major Accidents that we have studied. The explosion occurred when a distillation column used to produce high octane fuel was filled with liquid due to a closed outlet valve. The overfilling caused pressure relief valves to open, and the contents of the column filled a blowdown drum with hot hydrocarbons. This drum then overflowed, and a geyser of hot liquid spouted from the open vent on the drum. The resulting vapour cloud was ignited by a diesel pick-up truck that was parked nearby and still running. The explosion killed 15 people and injured 170.
Why would we consider this explosion as one of the worst Major Accidents? There are three key points that have led us to this conclusion.
1. There were clear signals that the systems in place to prevent a Major Accident were not functioning as intended. These signals were not acted on.
2. The design and operation of the facilities ignored basic principles of inherent safety. Hazards were not eliminated that could have been eliminated, and people were placed in danger, that did not need to be there.
3. The culture at the refinery was poor. Operational practices deviated from the approved procedures, cost cutting had been carried out without due regard to safety and the management focus on safety was misguided.
In this Reflektion we will consider signals that were not acted on. In the next two Reflektions we will consider inherent safety and culture.
The Operator of the refinery was BP Amoco. The site had experienced 22 fatalities in the previous 30 years including two fatalities in 2004 and three near fatal injuries in 2003. BP Amoco used a verification system called getting HSE right (gHSEr) to audit their facilities. The 2003 audit indicated that incidents including fatal incidents could be linked to the reduction in maintenance spend. In the summary of the 2003 audit, it was stated that the condition of the refinery is poor. The 2004 audit indicated the refinery was in complete decline and urgent and far-reaching efforts were required to improve safety. In the summary of the 2004 audit the auditors stated there was widespread tolerance of non-compliance with basic HSE rules. The BP employee survey in 2004 indicated that critical failures were not attended to and that pressure for production and cost reduction were the major causes on accident. In February 2005, the Safety manager at the site wrote, ‘I truly believe we are on the verge of something bigger happening.’ There was however some good news with the lowest recordable injury rate at the site in 2004.
The management did not act on these signals that were obvious even without the benefit of hindsight. Keep following this series of Reflektions and we will explain why.