The Weekly Reflektion 28/2025
On receiving a message of a new incident at a refinery, Trevor Kletz, a renowned safety adviser, told the messenger that he needn’t send an incident report since he already had a similar report in his files. Learning from our mistakes and implementing measures that will prevent Major Accidents remains a major challenge for all industries working with hazardous materials at high pressure and temperature. We have still a way to go.
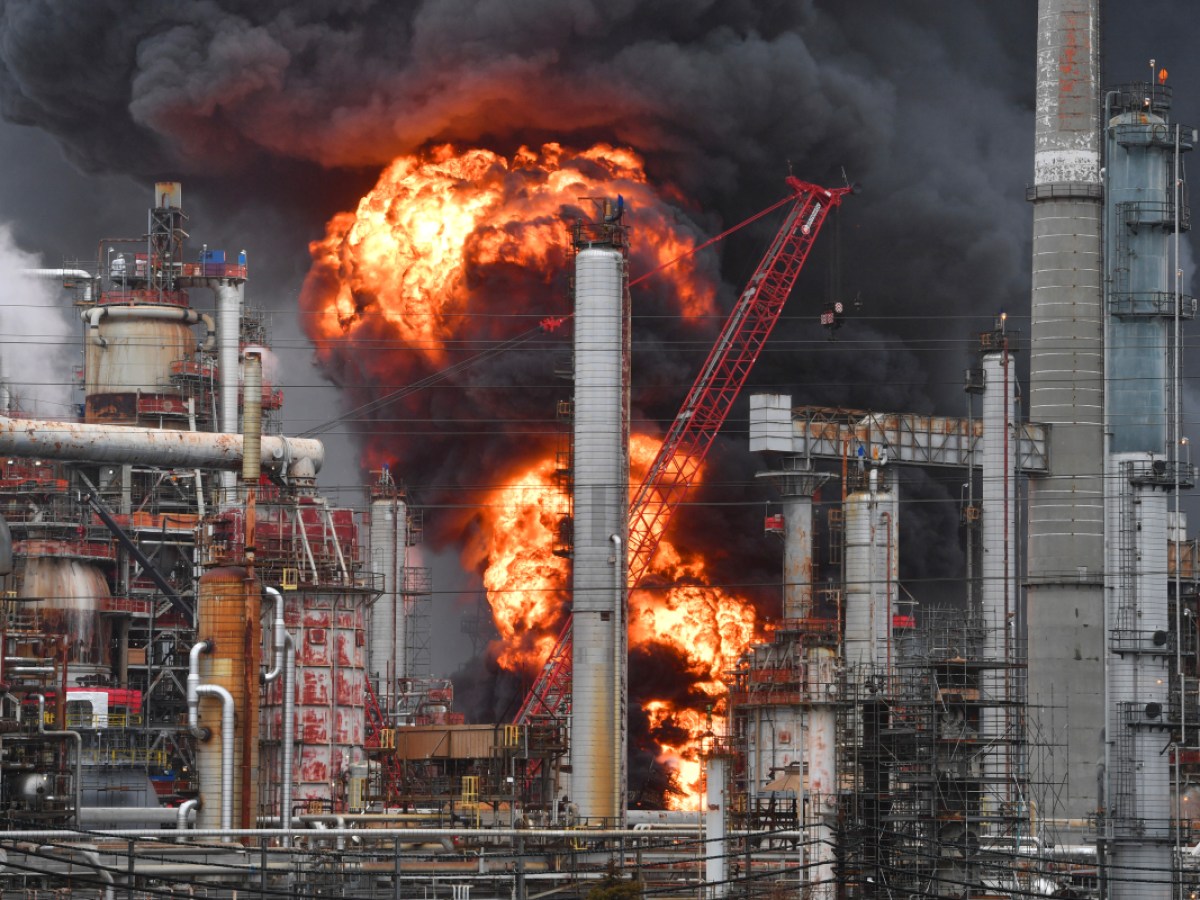
Are you trying to learn?
On 23rd March 2005, the Texas City refinery was being started up following a maintenance shutdown. The outlet valve from a distillation column was inadvertently closed, the column overpressured and overflowed to a local vent. A diesel truck with the engine running ignited the vapour cloud. 15 people were killed and 180 injured. The Texas City refinery disaster has been the subject of several Reflektions.
The Marathon refinery in Martinez, California, was in the final stages of restarting a newly modified unit designed to produce renewable diesel. The project was part of a broader push to reduce emissions and rebrand the facility as part of the green energy future.Engineers and plant operators had been working tirelessly to bring the hydrodeoxygenation unit online. During the start-up on 19thNovember 2023 a tube on a fired heater ruptured releasing a mixture of renewable diesel and hydrogen. There was a fire that seriously injured one of the refinery employees.
A manual valve was open when it should have been closed. Dieselwas partially diverted through this valve around the heater resulting in inadequate flowrates through the heater. A flowmeter downstream of the heater was incorrectly positioned and measured both the heater flow and diverted flow so the production operators were unaware of the low flow. The air supply to some of the heaters’ burners was also blocked resulting in incomplete combustion of the fuel in the heater. This led to poor convection within the heater. The unburnt fuel was reignited in the heater upper sections, a process called afterburning, and this combined with the poor convection led to overheating of the tubes in the heater. The process operators had noted that there were high temperatures in the heater, however there was insufficient flame detection and combustion monitoring that would indicate afterburning.
The refinery personnel investigated the problem, and a process operator was sent to a local control panel to turn off some of the heater burners. As he stood at the control panel a tube in the heater ruptured and the resulting explosion and fire seriously injured the operator.
Reading the Chemical Safety Board (CSB) report on the Martinez facility fire gave me a ‘déjà vu’ experience from the CSB report on the Texas City refinery disaster. A valve in the wrong position, operators not aware of the extent of the process problems, inadequate monitoring of critical equipment, and people in the proximity of the facilities during a start-up. The CSB concluded that Marathon failed to have sufficient oversight of their facility and failed to ensure the Martinez refinery complied with their corporate standards. The known deficiencies at Martinez contributed to the explosion just like the deficiencies at Texas City refinery, where BP failed to ensure corporate oversight.
The cost of the fire was USD 350 million and one person was subjected to third degree burns over 80% of his body and spent 6 months in hospital. He will bear the scars for the rest of his life. This is the price we pay when we fail to learn.