The Weekly Reflektion 38/2023
Inherently safer design has several basic principles that if adhered to will save lives. Keep the hazardous material contained and if it does have to be released then do it in a safe way. Keep the people away from hazardous materials and hazardous situations. If no one is there, then no one gets hurt. If you want some ideas on how to get it right, try looking at examples where others got it wrong and for goodness’s sake learn.
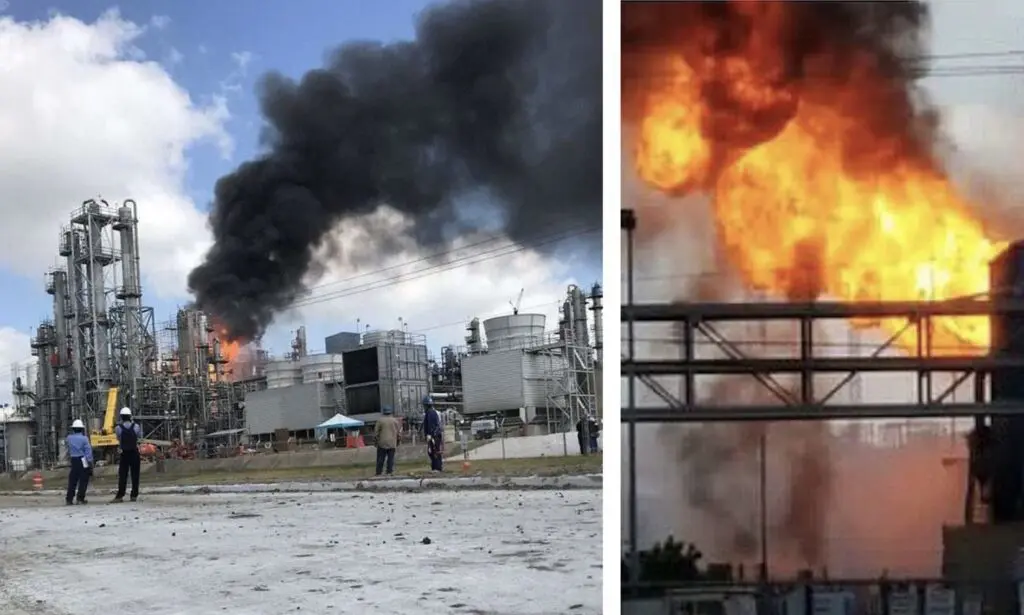
How bad does it have to get before we learn how to prevent Major Accidents?
Our attention was recently drawn to a Chemical Safety and Hazard Investigation Board (CSB) report from 2018. The first two safety issues noted were:
-Emergency Pressure-Relief System Discharge Design
-Presence of Non-essential Workers During Startup and Upset Conditions
You know when you get that ‘déjà vu’ feeling, it stimulates interest and you think, ‘This is a report we need to read and reflect on’. The similarities with the Texas City Refinery disaster 23rd March 2005 are chilling. At Texas City 15 people were killed and 180 seriously injured. Two of the main factors that resulted in the tragic loss of life were the design of the pressure relief system on the isomerization tower, and the presence of construction workers in temporary office containers during startup.
On 19th May 2018 the Kuraray ethylene and vinyl alcohol copolymer (EVAL) plant in Pasedena Texas was being started up after a maintenance shutdown (turnaround). Problems were experienced in one of the reactors that led to a high pressureand alarms were activated in the Control Room. The problems continued until the pressure relief system operated and released about 1000 kgs of ethylene vapour. The pressure relief system consisted of a pressure relief valve with adischarge through a horizontal pipe into the atmosphere around the reactor. At that time construction work was still ongoing including welding work. The ethylene ignited and the resulting fire injured 23 workers. Some of the injuries were caused by people jumping down from height to escape the flames. Some of the people could not escape quickly as they were still attached to fall protection equipment. Amazingly there were no fatalities.
The ethylene discharged from the relief system was not routed to a safe area. This is not an inherently safe design. Had the ethylene been disposed of to a remote flare then the workers would not have been affected by the pressure relief. There had been several releases of ethylene from the pressure relief systems on site and a Hazard review team had raised a concern on the danger of ethylene vapour explosions and made a recommendation to improve the relief systems. The management did not instigate any remedial measures nor document its reasoning for why no action was taken.
What were the construction people doing on site while a start up of the plant was ongoing? This is one of the most critical phases for a facility processing hazardous materials. The golden rule is to keep everyone away and only allow essential personnel on site for specific activities during the start-up phase. At Kuraray it was claimed there was an unwritten safety practice to exclude non-essential personnel from the site during a start-up. This unwritten safety practice was not followed on this occasion, and we wonder why.
In the next two Reflektions we will look more closely at this incident, why it happened and why the learning process failed.