The Weekly Reflektion 37/2021
Isolation of Energy is of fundamental importance to control of work and the safety of people involved in any activities. The processes for isolation and de-isolation need to be concise and systematic and proper verification is required to ensure the processes are followed.
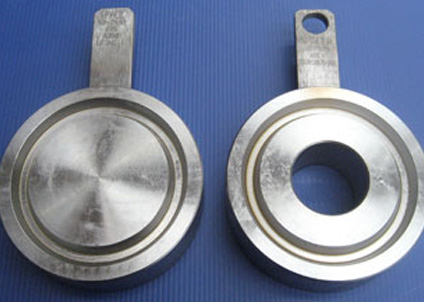
Do you have proper control of your isolations and de-isolations?
Major plant shutdowns are challenging and there is normally a push to complete the planned work on time and get the plant producing again. While enlightened companies have realised that undue pressure to start up can result in errors and shortcuts that lead to accidents, many companies still consider the main success criteria as being minimum loss of production. During major plant shutdowns part of the work scope is internal inspection of vessels and tanks to provide assurance of their integrity. Internal inspections by people require isolations for man entry to ensure it is safe to work in the enclosed space. The isolations are either blinds, blank flanges and/or spades to ensure 100% isolation or pipework is disconnected and left open to a safe atmosphere. In some systems the pipework adjacent to the vessel/tank is designed with spacers that can be removed and replaced by spades. See illustration. This is particularly common in thick wall pipe systems (e.g., high pressure systems) where there is little flexibility in the pipe to insert a spade.
During a planned shutdown on a facility, a high-pressure separator had been spaded off for an internal inspection and to change out the demister system on the gas outlet. The work was completed and the separator de-isolated. The systems were then tested for leaks successfully by using nitrogen/helium. The process facilities were then line-walkedto check the system status and then started up. After a few minutes it was noticed that there was no flow through the separator and the pressure upstream of the separator was high. An investigation was carried out and the blockage point identified was the inlet flange to the separator. There seemed to be a spacer installed in this flange since there was a hole in the tag. During the shutdown the spacer would have been changed out with a spade which does not have a hole in the tag. The spacer should have been re-installed as part of the deisolation.
The process facility was shut down again, de-pressured, purged with nitrogen and the ‘spacer’ removed. The spacer turned out to be a spade. The spade had been installed to meet the man entry requirements however the deisolation process had not been thorough to ensure this spade was removed and replaced with a spacer. On further investigation it was discovered that someone had drilled a hole in the tag on this spade and several others in order to hang them up neatly in the stores. There had been a ‘Keep it Tidy’ campaign a few years before and there were comments on the storage area for blind flanges and spades. Problem solved on the housekeeping; problem created on the control of isolations.
How do you ensure that the correct isolations are put in place? How to you ensure that these isolations are removed when the work is complete? Do you have control?