The Weekly Reflektion 27/2021
Following an incident, we often hear these words from the management “if only the operational team hadn’t done that” and “why didn’t they stop the job?”. What do these statements say about the management’s perception of risk management?
Where should we focus our efforts on preventing incidents?
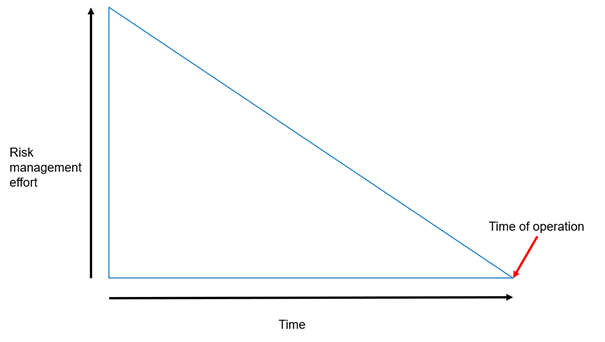
Recently we have noticed that several companies have had ‘Stop the job’ campaigns to focus on members of the offshore team’s important function of preventing dangerous situations developing. These campaigns are often triggered by the thought that if only the offshore personnel had done this, or not done that, then the incident would not have happened. Although there is no doubt that stopping the job is an important barrier it should not be allowed to completely derail the risk management discussion.
In terms of hours of effort, the risk management discussion should be front-end loaded. Starting in the equipment/system design phase with identification of hazards, consideration of failure modes, and assessment of consequences. Application of inherently safer design principles. Ensuring there are at least two barriers are in place to prevent catastrophic events and considering the possibility of human error during any operation. This design period is demanding, both in terms of involvement of the necessary disciplines, understanding which standards should be applied and how to apply them, and management of the interfaces between the different parties involved. The reliability of the individual parts, and the collective parts should be considered to ensure that the final product is satisfactory. The operational environment factors also need to be considered. The design should be the subject of study by both discipline experts and operational people in a systematic HAZOP process.
Once the design is ready, the construction phase should be monitored to ensure the necessary quality criteria are met. This is followed by commissioning and acceptance testing in real operational conditions to ensure functionality is appropriate and compliant with the design. Any failures along the way will need to be corrected and risk management processes applied. Potential hazards and hazardous situations and operational barriers should be covered in the user manuals and operational procedures. The people using the equipment need to be instructed on the operation and their competence continually reassessed and developed.
From the above description, the amount of effort needed to get equipment and systems into the operational environment, ready for use is considerable, not to mention the effort needed to maintain both the equipment, the documentation, and the competence of personnel as equipment is used, experience gained, and perhaps modifications made.
In the event of an incident, the sentiment of questioning why the operational team did, or did not do something to prevent something happening should be complemented by considering why the technical, operational and organisational barriers put in place earlier in the process failed to stop the incident. In addition, asking why the people thought what they were doing was OK is important, as they were certainly trying to do their best. When an organisation is overly focussed on the operator intervening when something goes wrong then it may not have enough focus on ensuring the operator is not put into a position where he/she must intervene. The primary focus of the management should be to design out the potential failure mechanisms.