The Weekly Reflektion 22/2021
Risk Assessments are often held using a meeting format and sometimes the basis for the assessment is the assessment carried out last time. During the meeting mitigation measures are identified and included in the action plan. Some of the measures identified may appear sensible in the moment, but do they actually reduce the risk?
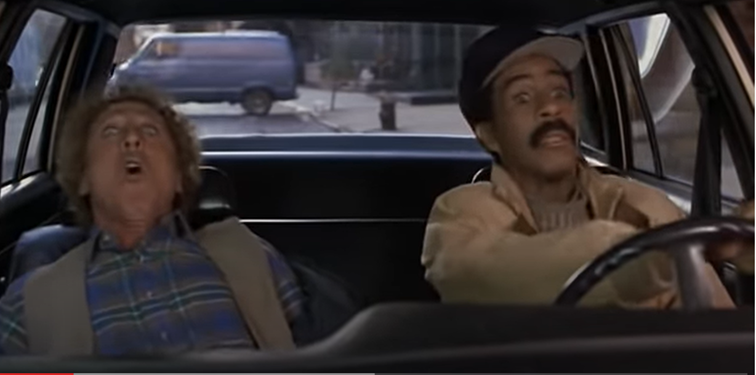
Gene Wilder (left) and Richard Pryor (right) in the Car Chase in the film See No Evil, Hear No Evil
Do you have risk mitigation measures that look good but do little to reduce risk?
In the film ‘See No Evil, Hear No Evil’, Gene Wilder plays Dave who is deaf and Richard Pryor plays Wally who is blind. In the film they witness a murder, Dave sees the legs of the murderer and will recognize them again and Wally remembers her perfume. The murderer and her accomplices are out to get Wally and Dave to prevent them helping the police with their enquires. During the ensuing chase Wally and Dave steal a police car and Wally ends up in the driving seat. Since there is no time to change places, Dave gives Wally instructions on where to drive. During the car chase Wally turns to Dave and ask, ‘How am I doing?’. Dave replies, ‘Don’t look at me, watch the road!’. Wally assures him with the words, ‘Ok, if it makes you feel better’.
Sometimes the risk mitigation measures that we identify in risk assessments make us feel better yet in reality may not actually have any risk reduction effect at all. In fact, they can have the opposite affect by stopping the discussions around the issue and giving a false sense of security. When several risk reduction measures are noted, it may also give the impression that the risks have been assessed properly hence give the people carrying out the work that ‘feel good feeling’.
I was involved in the planning of a production shutdown on an offshore installation. The scope of the inspection, maintenance and modification work was extensive and many of the process vessels were to be inspected internally. This required fitting mechanical blinds or spades to ensure positive isolation before people could enter the vessels. Before the process systems could be restarted, they had to be tested and for this process we used a mixture of nitrogen and helium to check any disturbed flanges for leaks. At the risk assessment one of the mitigation measures identified was to ensure the system pressure relief valve was installed on the system before leak testing started. During the testing one of the heat exchangers was subjected to excessive pressure resulting in an instrument fitting being blown off, narrowly missed a technician working 20 meters way.
The investigation into the incident revealed that the pressure relief valve on the heat exchanger was designed for thermal relief (an increase in pressure above design pressure due to increase in temperature). The capacity of the relief valve was significantly less than the rate the compressor in the nitrogen/helium skid could deliver. The overpressure system on the nitrogen/helium skid had not been adjusted following a test on a system with a higher pressure.
A pressure relief valve on a system may give you that good feeling but will it cope with the required flow for all the likely scenarios? Have you thought about both process scenarios and commissioning and start up scenarios?