The Weekly Reflektion 15/2021
Sometimes in your career you will hear about incidents that you will never forget. It may be a major accident that gets a lot of publicity. It may be an incident related to your discipline and that you have a good understanding of the details. It may be an incident that gives you that OMG feeling. The Hydrocracker Explosion and Fire at BP Oil, Grangemouth Refinery on 22nd March 1987 was one of mine.
Are you sure your High-pressure Low-pressure (HP/LP) interfaces are designed properly?
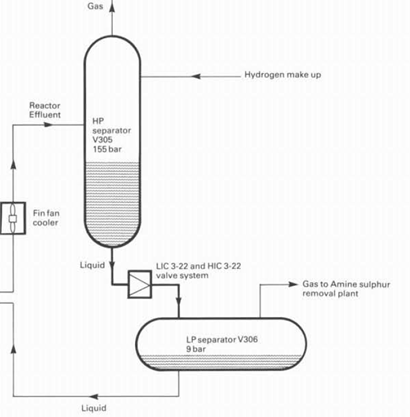
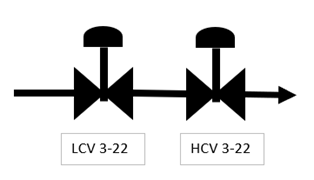
The valve system
On 21 March 1987, the hydrocracker unit at the Grangemouth refinery was being started up after a routine shutdown. During the recommissioning process high pressure hydrogen was circulated through the high-pressure (HP) separator to warm up the system. During this process, the liquid level control valve (LCV 3-22) and a manual valve (HCV 3-22) between the separator and the low-pressure (LP) separator, were closed. The control valve also functioned as a production shutdown valve.
Liquid naphtha was introduced into the HP separator and the manual valve was opened ready to start the process. A plant trip occurred, and the unit was held in a standby condition. During this period the control room operator decided to test the control valve to check it was OK after the shutdown. He opened and closed the valve several times. Hydrogen at 130 barg flowed through to the LP separator. The LP separator was designed for 9 barg. The LP separator failed catastrophically, and the resulting explosion killed a person working on the site. The explosion was heard 30 km away and a piece of the separator weighing 3 tonnes was found on the foreshore 1 km away.
The overpressure system on the LP separator was designed for a fire relief case, that is the pressure increase from a fire around the separator boiling the contents. The system had also been checked for a case with the LP separator outlet valves closed and liquid naphtha flowing from the HP separator. The system was not designed for high pressure hydrogen flowing through the control valve into the LP separator. This is often termed ‘gas blowby’.
A low liquid level trip was originally installed in the HP separator that would shut the outlet valve (LCV 3-22) if there was a low liquid level in the separator. This trip had been disconnected a few years previously as part of a modification. The level measurement in the HP separator did not measure the correct level in the HP separator due to a problem with the chart recorder.
The potential for ‘gas blowby’ had not been identified in the HAZOP carried out as part of the design.
Cyril F. Parry, in his book ‘Relief System Handbook’ writes:
‘It is the prime responsibility of the process engineer to ensure that his or her process plant is adequately designed for the expected pressure and temperature conditions; and that any equipment under pressure is protected by a reliable pressure safety device that will limit the pressure rise to permissible level. Following installation, the device must be carefully maintained to ensure that it continues to work effectively throughout its service life’.
Nice One Cyril!!
How do you know if your process is adequately designed for pressure?